La page "Présentation" de l'INRIA
espace enables to visualize various workspaces
for a 3-RPR planar parallel robot, and to plan motion for this kind of
robot, insuring that the trajectory always lie inside the robot workspace.
Let C define a given point on the moving platform.
These workspaces are:
- constant orientation workspace. This workspace is defined as
the region which can be reached by C
when the orientation of the moving platform
is kept constant.
- maximal workspace,
which is defined as the
region which can be reached by C with at least one orientation.
- inclusive workspace, i.e. the
region which can be attained by point C with at least one orientation in a
given range.
- total orientation workspace,
i.e., the region which can be reached by point C with every orientation
of the platform in a given
range.
- dextrous workspace,
which is defined as the region
which can be reached by point C with any orientation of the platform.
Free source codes are available under Free Software Society
conventions through anonymous ftp
(download here for
Sun, download here for Linux).
This software is provided "as is" without warranty of any kind. In no
event shall INRIA be liable for any loss of profits, loss of business,
loss of use or data, interruption of business, or for indirect, special,
incidental, or consequential damages of any kind, arising from any error
in this software.
Window system: X
Type: sources
Language: C
OS:Solaris,linux
Total number of lines: around 27000
Size of the executable: 3.5 Mo (Solaris),2 Mo (linux)
Output: display, files, graphic output in xjpdraw format
espace user's manual
Version 0.1
July 26, 1995
J-P. Merlet
INRIA Sophia-Antipolis
France
E-mail: Jean-Pierre.Merlet@inria.fr
espace enables to visualize various workspaces
for a 3-RPR planar parallel robot, and to plan motion for this kind of
robot, insuring that the trajectory always lie inside the robot workspace.
It is an implementation of the
algorithms described in [1].
Let C define a given point on the moving platform.
These workspaces are:
- constant orientation workspace. This workspace is defined as
the region which can be reached by C
when the orientation of the moving platform
is kept constant.
- maximal workspace,
which is defined as the
region which can be reached by C with at least one orientation.
- inclusive workspace, i.e. the
region which can be attained by point C with at least one orientation in a
given range.
- total orientation workspace,
i.e., the region which can be reached by point C with every orientation
of the platform in a given
range.
- dextrous workspace,
which is defined as the region
which can be reached by point C with any orientation of the platform.
The 3-RPR robot is constituted of a moving platform connected to the ground
through three revolute-prismatic-revolute kinematic chains
(figure 1).
Figure 1:
The 3-RPR robot
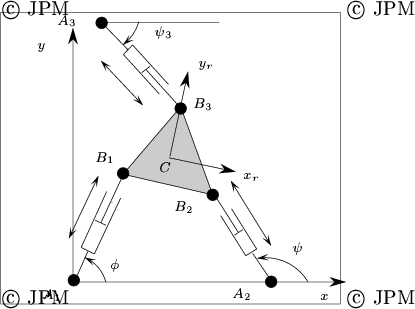 |
The mechanism is defined via two structures:
struct quatre_barres
{
float p;
float r;
float s;
float c;
short int coupler; /* 1 if the coupler exists */
float a;
float b;
float sgamma; /*sine and cosine of gamma */
float cgamma;
};
struct cinq_barres
{
struct quatre_barres sous_4barres;
float or[2];
float r3;
}
Indeed the 3-RPR robot is constituted of a four bar mechanism
whose elements are defined in figure 2, with an additional
link whose attachment point to the ground A3 has coordinates stored
in or and whose length is r3.
Figure 2:
A four bar mechanism
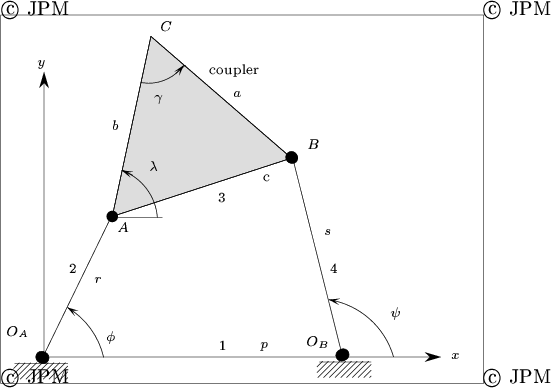 |
Therefore the three length of the chains are r, s, r3.
To use this program you need to define the structure of the robot in a
file with the following syntax
A file defining a 3-RPR mechanism has the following syntax:
5-barres
p
r
s
c
1
a
b
sgamma
cgamma
or[0]
or[1]
r3
The value of the leg lengths defined in this file are only used
to display the robot in one one of its configuration when running the
program. To specify the minimal and maximal values of the leg lengths you
need to create another file which contain these values. For example the
file:
2 8
5 25
10 25
specify that the minimum value for r
is 2, its maximal value 8, then you got
the value for s and r3.
To run the program use the command:
espace [mechanism file] [extremal lengths file]
The mechanism will be displayed in a nominal position.
By definition the vertices of the moving platform are called B1, B2, B3
which are connected to the leg of length r, s, r3.
This buttons enable to compute the maximal workspace for the reference point
B3. After having clicked in this button you should see the drawing of the
maximal workspace (this may take some time, up to 30s for very complex
cases). The boundary of the maximal workspace is displayed in green. Inside
the region you may see also various curves in different colors. These
regions may define sub-maximal workspace, i.e. maximal workspace according
to an initial assembly configuration. To check that put the cursor in the
screen, on top of the display you will see the current location in the
reference frame of the robot (whose center is located at A1), and the
possible orientation of the robot for the current location (note that the
orientation is defined as the angle between Ox and B3B1).
The possible orientation is a list of intervals. You may notice
that when crossing a curve in the maximal workspace, the
number of possible
orientations intervals will vary.
This button is used after having computed the maximal workspace and enable
to save a description of the workspace in a file. This description has no
interest for the user's but will be used by espace when planning a
trajectory. If a file describing the maximal workspace has been saved the
computation time for planning a trajectory will be drastically reduced.
This button is used to display the three maximal workspaces
when the reference point is defined as B1, B2, B3.
This button enable to compute the workspace of B3 when the orientation of
the moving platform is constant. Give a value for the orientation angle
(the rotation angle
is the angle between Ox and B1B3) and press Return.
This button enables to compute the inclusive orientation workspace for B3,
i.e. all the position of B3 such that the possible orientations of the robot
has an intersection with an orientation range.
For example if the range you have defined is [300, 310]
and the possible orientation of the robot is [270, 305]
for a given position of B3, then this position is inside the
IOW. Give the range as two angles
in degree, followed by a return.
This button enables to compute the total orientation workspace for B3,
i.e. all the position of B3 such that the possible orientations of the robot
include an orientation range.
For example if the range you have defined is [300, 310]
and the possible orientation of the robot is [270, 315]
for a given position of B3, then this position is inside the
TOW. Give the range as two angles
in degree, followed by a return. Note that giving an orientation range
of [0,360] enables to compute the location of B3 such that every
orientation is possible, i.e. the TOW is the dextrous workspace
of the robot.
The robot will be displayed
if you give the position of B3 (two coordinates) and the orientation
(in degree). The color of the legs will be be red if the link length
is outside the allowed range and blue otherwise.
When clicking in this button you will be able to plan motion for the
robot.
First the program will compute and display the maximal workspace of
the robot. Note that if you have previously computed this workspace
and saved it, then the motion planner will directly use the file. Then
an auxiliary computation is done (which is computing a skeleton as
described in [1]).
Then a new window will appear where you can indicate a start and a goal
configurations. First introduce the start configuration, followed by a
Return, then the goal configuration, followed by a Return.
The planner will then try to compute a trajectory: by default the
planner look for the shortest trajectory. You can change this by
clicking in
the Priority button: if the priority is length the planner
will look for the shortest path, if the priority is orientation
the planner will try to preserve the orientation (for example if the
start and goal configuration have the same orientation it will look
for a trajectory on which the orientation remains the same). If the
priority is circular the planner will look for a
circular trajectory if the start and goal have same orientation, in
which the constant orientation workspace will be displayed.
You can also define a desired trajectory together with a priority
in a file in which you define the three coordinates of the start
points, the three coordinates of the end point and then a keyword for
defining the priority, either length or orientation.
Note that when a trajectory is displayed the leg lengths are also
displayed on top of the screen.
The Read Trajectory File enables to display a pre-computed trajectory.
The Redraw button enables to redraw the trajectory. By using the
Slowness button you can adjust the velocity of the robot, the
greater the value, the slowest the velocity.
After having computed a trajectory you can save it using the
Save trajectory button.
These buttons may be used to modify the location of point OA on the
screen or to zoom the drawing. To zoom give a scale factor followed by
a Return in the Zoom window. A number lower than 1 will enable to
reduce the
size of the display. To indicate a new position of OA
give its new screen coordinates in the window, followed by a Return.
The Clear button erase the screen, the Time button
indicates the computation time for the last action, the Time(s)
button will display the computation time of the skeleton.
The Debug button is used to debug this program. Although not
very useful for a user it can be used to display the geometrical
element which appear during the computation of the workspaces: for
example the sextics, circles will be displayed.
xjpdraw is a drawing editor which accept external inputs and is
available via anonymous ftp.
This button is used to save in xjpdraw format
what is currently on the screen.
- if you have computed the maximal workspace for B3
the name of the generated files are:
espace_maxi.jpd (with only the border of the maximal workspace)
and espace_max_entier.jpd which contains the border but also
the internal arc.
- if you have computed the three maximal workspaces
the name of the file is espace_max123.jpd
- if you have computed the constant orientation workspace the name
of the file is espace_orientation_[value].jpd, where value is the closest integer to the orientation angle.
- if you have computed the IOW the name of the file will be
espace_maxi_angle_[value1]_[value2].jpd where value1,
value are the closest integers to the angles of the range
- if you have computed the TOW the name of the file will be
espace_teta_angle_[value1]_[value2].jpd where value1,
value are the closest integers to the angles of the range
- if you have displayed a robot the file name will be
robot_configuration.jpd
To use one of the graphical output files, e.g. pos.jpd use xjpdraw with the command line:
xjpdraw -X 6 -Y 6 -F pos.jpd
where the numbers following the X and Y argument are the width and height of
the box which will contain the output data.
Here are some examples of drawing generated.
Figure 3:
Example of maximal workspace
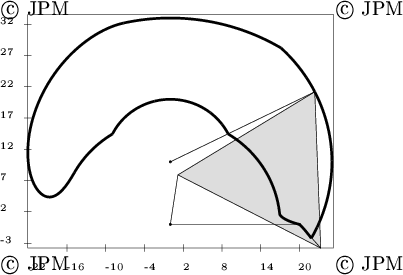 |
Figure 4:
Example of IOW
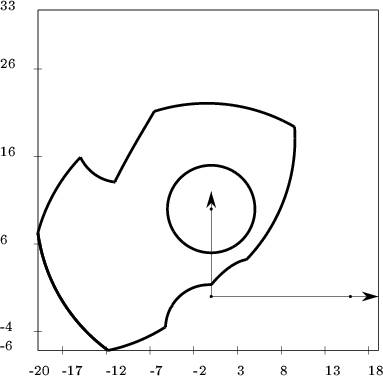 |
Figure 5:
Example of TOW
 |
You can also use a command language for controlling the behavior of the
program.
To do that you write a file and run the program with the command
espace -C [command file]
If instead C you use I then no window will appear, the
program will just execute the command file without displaying any
result on the screen. You will have a similar behavior if you put at
the start of your command file the keyword hidden.
One of the first instruction should be the definition of your robot
with:
robot "robot file name"
Then you define the minimal and maximal leg length with:
length "5 20 5 25 6 30"
where 5, 20 define the length range for link 1 and so on.
When this instruction is encountered and a robot has been defined the
program will compute and display the maximal workspace.
This language has variables whose names are %0, %1 and so
on and vectors whose names are %v0, %v1 and so on.
In this language you have loop instructions (while, for),
conditional instructions and you can perform operation on the
variable, see the xjpdraw manual for more details.
You can compute the possible orientation angles for a position as:
%v0[0]=1
%v0[1]=2
%1= angle_limite ( %v0 , %v1 , %v2 )
%v0 define the coordinate of the position and %1 will
contain the number of orientation intervals, the start of the
intervals being put in
%v2.
You can define an orientation with:
orientation= %10
You can test if a point is inside the workspace with
%5= point_in_space ( 10, 20, 300 )
where the three number define the position and orientation.
You can compute a TOW with:
variable= espace_orientation_total variable variable
where the two last variables define the orientation angle range in degree.
You can compute a IOW with:
variable= espace_orientation_inclusive variable variable
where the two last variables define the orientation angle range in degree.
You can compute a constant orientation workspace with:
variable= espace_orientation variable
where the last variables define the orientation angle in degree.
In all these cases the first variable contains the number of zone of
the computed workspace.
You can display information on the screen during the execution of the
program with:
info " string to be printed"
For the motion planning you define the start and goal configuration
with:
start u1 u2 u3
goal v1 v2 v3
where the u's and v's may be either numbers or variables and define
the position and orientation of the robot.
You can set the priority with
priority_length, priority_orientation.
You can look for a trajectory with:
%1= mode find_trajectory
In return the variable will have the value 1 if a trajectory has been
found.
The current result of the computation could be saved in xjpdraw
format with:
save "file name".%1 "auxiliary file name".%2
The result will be in general save in the file
file name".%1
but if two files are to be saved the second name will be used.
To quit the program use quit.
- 1
-
Merlet J-P. and Mouly N.
Espaces de travail et planification de trajectoire des robots
parallèles plans.
Research Report 2291, INRIA, 1994
GET IT!ftp://ftp-sop.inria.fr:/pub/rapports/.